Enhancing safety in lithium-ion batteries
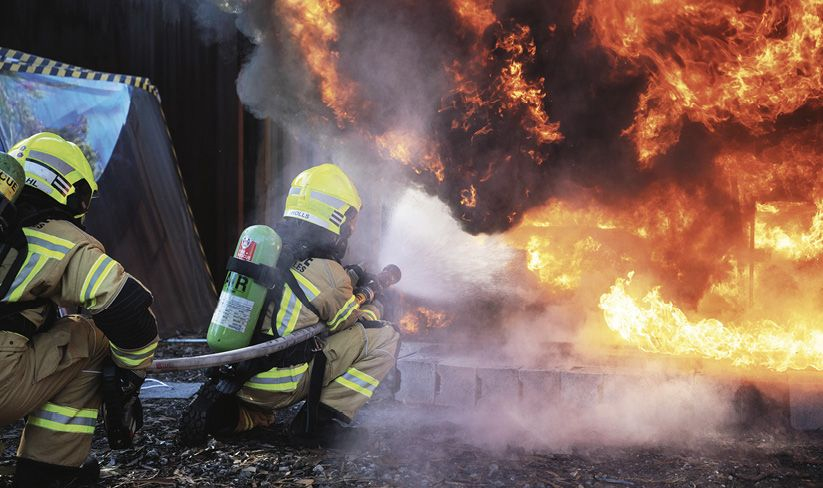
Battery manufacturers are placing an ever-greater emphasis on safety design to prevent fires.
Photo: Fire and Rescue NSW
From pv magazine print edition 5/24
News reports about battery fires in grid and mobility applications make for lurid headlines but a closer look at the data reveals a far more nuanced picture. Even with billions of lithium-ion battery cells in use today across electric mobility, stationary storage, and portable electronics applications, the rates of catastrophic failures involving fire or – in the worst-case scenario – an explosion, remain low.
Safety differences are notable across diverse applications, however. Fires in micro-mobility products have been on the rise. The situation is particularly dire in dense urban areas, where many people, such as delivery workers, rely on e-bikes and e-scooters for their livelihoods. Less quality control, fewer safety regulations, and the use of unapproved aftermarket components are often quoted as the reasons behind these fires. On the other hand, electric vehicles (EVs) and grid-connected systems are subject to stringent safety testing and certification and both have strong safety credentials. For instance, EVs have significantly fewer thermal incidents than combustion-engine vehicles.
Lithium-ion technology’s overall safety record in energy storage applications is strong and continuously improving, according to data collated by the Electric Power Research Institute (EPRI). Since the first battery energy storage system (BESS) installations about 10 years ago, the EPRI BESS Failure Event Database has recorded roughly 85 events worldwide, ranging from minor to major. Over the past four years alone, there have been, on average, 10 such failure events annually, even as global battery deployments have increased 20-fold. In the United States, six battery failure events occurred in 2022 and seven in 2023. To put that into perspective, according to the Wood Mackenzie Q1 2024 and 2023 Year in Review, roughly 7.9 GW of grid-scale energy storage was installed in the United States in 2023. This was reported to be a 98% increase over the total installed capacity in 2022.
“So, while the number of incidents roughly stayed constant, the number of installed units vastly increased, lowering the failure rate of these systems,” said Carrie Kaplan, team lead for energy storage safety and energy systems at compliance testing group DNV. “This is largely due to the lessons learned from the failure of events directly influencing the codes and standards developed for these systems.” There is a large family of codes and standards, such as IEC, UL, and IEEE, that impose clearance and separation distances, fire suppression, and venting and explosion control for BESS, among other requirements intended to reduce the risk of failure. As a result, battery manufacturers are placing an ever-greater emphasis on safety design of their products, with a special focus on prevention, as well as fail-safe mechanisms.
Complex task
However, an increasing range of use cases and the technology’s importance in the global decarbonization landscape highlight the need to enhance lithium-ion battery safety and the understanding of potential failures even further. Namely, when battery-related incidents do occur, the cause is generally due to mechanical, thermal, or electrical stress or abuse. Mechanical abuse can involve an internal defect introduced during manufacturing or damage caused to the cell by crushing or penetration. In a thermal abuse scenario, a battery undergoes thermal shock (for example, if exposed to an external fire) with dangerously high temperatures causing the cell components to break down. Finally, electrical abuse, the most frequent cause of acute cell failures, occurs when a battery is subjected to conditions such as overcharging, over-discharging, or external short circuits.
All these issues can lead to a dangerous phenomenon called “thermal runaway,” which involves sudden and significant battery cell temperature increases. The heat can then propagate from cell to cell throughout the battery pack, escalating the hazard. Eventually, the affected cells start venting toxic and flammable gases which can then ignite and cause a fire or vapor cloud explosion. First responders had previously mistaken these white vapor clouds for steam or smoke but their composition means they can be more damaging than the initial fire.
“Despite various claims, one of the still-not fully understood, and thus riskier aspects of lithium-ion battery technology is the behavior during thermal runaway,” said Wojciech Mrozik, a Faraday Institution senior research fellow at Newcastle University, in the United Kingdom, and member of the SafeBatt: Science of Battery Safety project. “For instance, we still don’t fully understand the composition of vapor cloud (off-gas).” He argued that the safety of lithium-ion batteries has seen significant advancements but there remains a critical need for further research, particularly in new materials, such as non-flammable electrolytes or solid-state batteries, as well as battery designs that reduce the likelihood of thermal runaway by protecting against external factors that can lead to failure.
“Addressing battery safety issues effectively requires a multidisciplinary approach that brings together several disciplines and experts,” said Mrozik. He added that integrating more sophisticated diagnostic tools that can monitor battery health in real time and predict failures before they occur, is also essential.
Well-designed hardware and software is critically important. For instance, poor battery pack design or a poor battery management system (BMS) can result in some cells being overcharged. Such risks have been reduced, over time, through product engineering and controls while failure mitigation and prevention have been improved. Jan Figgener, senior battery expert at German software developer Accure Battery Intelligence, argues that battery safety comes in four layers. First, cells must meet high quality standards which can be ensured by end-of-line tests such as capacity and impedance tests. Second, the system design should prevent faults in one cell or module from starting a chain reaction for the whole storage system. Third, the BMS is supposed to ensure safe operation within defined voltage, current, and temperature ranges. The fourth layer, predictive battery analytics in the cloud, is used to identify faulty cells and incidents before they occur, based on existing BMS data, enabling a condition-based and predictive asset management strategy.
“Due to the limited computational capability of BMS, they cannot detect all safety-critical developments,” said Figgener. “This is where cloud analytics is able to provide an additional, much-needed safety layer. Cloud computing is able to take the BMS data, reference massive global datasets, and use battery models and machine learning algorithms to compute safety parameters and send alerts.”
Work not done
BESS diagnostics is one of the latest software safety upgrades for stationary BESS and some would argue a necessary one, with operation and maintenance of batteries still at an early stage. The safety testing and standards need to be revised regularly to reflect technological advances in a rapidly changing industry like energy storage. DNV, which has been performing standard-based battery assessments, as well as nonstandard and research testing for many years, points to the ongoing debate within the industry on how large scale fire tests should be performed and whether they accurately represent real-world scenarios.
“One of the current trends we are seeing is large scale burn tests that go above and beyond the current requirements,” Kaplan said. The goal is to force one entire BESS enclosure on fire and ensure the flames do not propagate to its nearest neighbor. This typically provides local authorities with a degree of comfort knowing that if a fire should occur, it will likely not escalate to more than one BESS enclosure. While the list of hardware and software lithium-ion battery safety upgrades is a lengthy one, the emergency response plan is often seen as the most important safety measure. “This is a guidance document specific to the project site that details what can go wrong with the BESS and what to do if that happens. It is mainly for first responders and any personnel working on-site to ensure their safety first and foremost, but to also protect the surrounding assets,” Kaplan said.
This content is protected by copyright and may not be reused. If you want to cooperate with us and would like to reuse some of our content, please contact: editors@pv-magazine.com.
<