https://www.pv-magazine.com/2022/11/19/weekend-read-elusive-longevity/
Weekend read: Elusive longevity
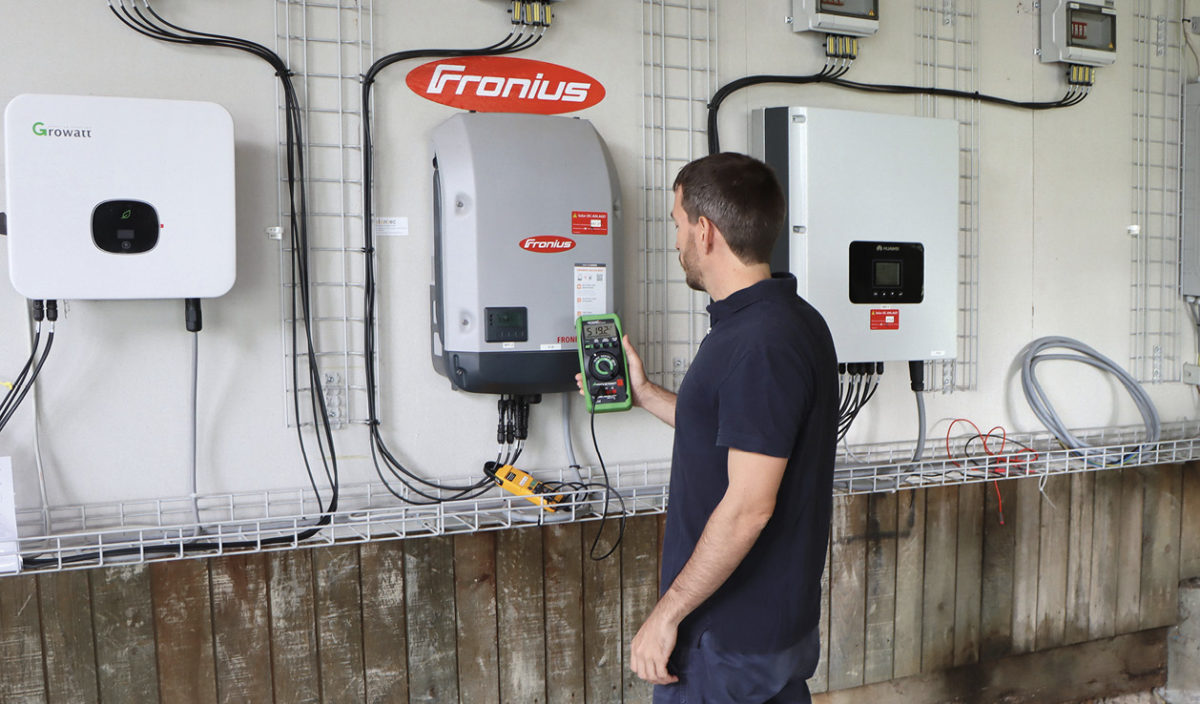
A team from the Bern University of Applied Sciences investigated the frequency of errors in inverters installed in Switzerland.
Photo: Bern University
From pv magazine 11/2022.
When Jens Heinzler enters a solar farm, he sometimes hears a shrill whistling noise from a distance. “A terrible noise,” says the managing director of Sun2Energy, a service provider for maintenance and technical management of photovoltaic systems. The noise comes from string inverters and while the exact defect isn’t always clear, Heinzler can tell that string inverters making this kind of noise will soon have to be replaced.
Such plants, whose operators have signed a maintenance contract with Heinzler, went online between 2006 and 2020. “Many are now causing trouble,” he says, and it is more often the inverters, rather than the modules, that are the source of this trouble. For string inverters, a malfunction often equals the end of the device’s life. And operators frequently need to replace all of the inverters in a project before the period of feed-in tariff guarantees expires.
pv magazine print edition
The latest edition of pv magazine considers the impact the Inflation Reduction Act will have on US solar and ponders where the resultant manufacturing sites will land. The situation is just the opposite in Germany, we discover, with PV investors piling up but few suitable sites left for solar farms. We also anticipate shortages in raw materials to drive the electric vehicle revolution, and the measures battery makers are taking to secure supply, and we ponder the effect the rise of TOPCon solar will have on the supply of its preferred encapsulant resin.
Heinzler and his team are not alone: inverters represent the Achilles heel of solar power plants in terms of malfunctions. A 2020 data survey by the National Renewable Energy Laboratory (NREL) shows that in the United States, about 43% of maintenance calls on PV systems are due to inverter malfunctions, and 35% of measured yield losses are due to inverter failures. In the same study, modules are responsible for only 2% of maintenance calls and only 1% of yield loss. With figures like these, the question arises as to the reason inverters are such a weak point in the chain. Experts seeking an answer to this question want to develop better predictive models and longer-lasting inverters.
Inverter lifetimes
A team from the Bern University of Applied Sciences evaluated inverter failure surveys from 1,280 PV systems with 2,151 inverters. Small private rooftop systems to large ground-mounted systems with central inverters were all represented in the Swiss study. After 15 years, half of the plants show inverters with their first yield-relevant errors.
However, there are also significant differences between devices. Manufacturer, installation site and the design of the inverter all play an important role when it comes to longevity. For example, inverters installed indoors saw their likelihood of survival drop from 100% to 75% after 13 years. Devices that were installed outside, largely unprotected from the weather, reached the same survival probability after just six to seven years. However, study author Christof Bucher also says that other correlations may have favored this very clear result.
What the scientists back up here with numbers is in line with Heinzler’s observations; whistling inverters are often installed in free-standing assemblies with devices fully exposed to the sun. “If the inverters can be mounted under the modules, they are at least somewhat protected,” Heinzler says. That’s an advantage, he says, because heat clearly affects the devices. Inverters are supposed to be protected by derating parameters that reduce inverter output according to temperature limits. During hot summer days, these are quickly reached, and internal components suffer greater stress.
Temperature change
“Aging is favored by environmental factors such as intense heat or high humidity,” says Todd Karin of the PV Evolution Labs (PVEL) testing laboratory in California. A particularly common defect in power semiconductors is bond-wire lift-off, often caused by intense heat. Semiconductors are soldered to a circuit board made of a material sandwich of copper and ceramic. During thermal cycling, the materials expand to different degrees. The bonding wire to which the semiconductor is connected cannot withstand these movements and subsequently breaks. This leads to short circuits and arcing inside the inverter.
The constant change from hot to cold can also cause the ceramics to begin to delaminate, Karin continues. This leads to impaired conduction of the semiconductor’s heat and, in extreme cases, to short circuits. Additionally, heat can lead to degradation of the silicone or ceramic insulators in the semiconductor socket. This results in electrical breakdown with short circuits, arcing, and fire hazards.
Exactly how the environmental influences cause degradation in the components is still unclear and is being investigated, for example, in Halle, at the Fraunhofer Institute for Microstructure of Materials and Systems, or IMWS. In a project that began in 2020, a group is working alongside inverter makers including SMA, Electronicon, and Merz Schaltgeräte. They have provided returned equipment and broken devices used under real conditions.
Degradation
The team is taking a closer look at the defective components to understand the causes and aging mechanisms. In addition, the researchers are studying working inverters that have been in use for many years under real-world conditions or have undergone accelerated reliability testing. To characterize the degradation mechanisms, they use methods such as non-destructive acoustic microscopy or lock-in thermography. “We get the components from different climates sent to us by the manufacturers,” says Sandy Klengel, group leader for evaluation of electronic system integration at Fraunhofer IMWS.
Klengel and her colleagues match the collected aging data with usage parameters and records of environmental conditions, asking questions such as was it often hot at the site? Or, was the inverter often running at partial load? In many cases, similar data is recorded by the inverters at the same time.
“In this way, conclusions can be drawn about different aging mechanisms due to enormous heat or high humidity,” says Klengel. The goal of the research project is to develop better predictive models for inverter degradation and reliability. Klengel is reluctant to make sweeping statements about the causes of component failures. The studies have not yet been completed and it’s too early to fully decipher the data.
Moisture-sensitive
But Klengel reveals this much: “Film capacitors are particularly susceptible to moisture,” noting significant differences between the manufacturers of the capacitors here as well. In addition, manufacturers are working on new designs for capacitor housings and encapsulation systems. But other components are also affected by aging mechanisms; chokes, circuit boards, power semiconductors and everything else in an inverter ends up in the lab.
“That transistors, or IGBTs [insulated-gate bipolar transistors], have faults, is something we observe less,” says Heinzler, who doesn’t point at one failure pattern either, noting problems range from repetitive self-shutdowns and power loss to capacitor issues. From his experience, capacitors and communications equipment are cited as the most common issues.
Popular content
Often, certain patterns can also be identified based on manufacturers and years of manufacture, which helps with troubleshooting particular issues. Batch numbers are also key: if the production dates of the same inverter type are a long time apart, it may well be that the manufacturer uses different suppliers, and the error pattern changes. To be on the safe side when buying inverters or assessing the risk of installations, buyers should therefore look at the inverters’ bill of materials, says Klengel of Fraunhofer IMWS. There are inverters on the market with high reliability and a 20-year warranty as well as resistant capacitors, she adds.
Multiple failures
String and central inverters have different failure modes. PVEL's Karin reports that string inverters have up to 30 times as many components as central inverters, greatly increasing the susceptibility to failure. In addition, inverters with higher power conversion are increasingly shrunk in size. The demands on string inverters are therefore enormous, he says. “Nowadays, you want to install string inverters with 150 or more kilowatts of power with two workers and without an auxiliary crane,” says Jens Heinzler.
The problem with higher power density is heat dissipation. Karin, therefore, sees added value in giving data analysts from a maintenance service provider access to various temperature sensors in the inverter. Virtually all power semiconductor modules would have such sensors built in. But not all inverter manufacturers ensure that end customers have access to the data. This data could even be used to predict the failure or borderline operation of an IGBT.
Design and architecture
It is not only the manufacturers’ design that affects the service life of inverters but also the way in which they were installed. Heinzler explains an extreme case with a PV plant built with 270 installed inverters, each with a capacity of just 9 kW. Even with a failure rate of just 1%, he says, you must replace equipment several times a year. Slightly more powerful devices would vastly reduce the number of components.
Central inverters, on the other hand, would have the longest life expectancy but would also require more maintenance. For Heinzler, the reasons for the higher life expectancy lie in the fact that central inverters have sophisticated ventilation systems and the interior is generously designed. Overheating is rarely a problem. But a protected installation site also has a positive effect on service life, says Heinzler. This protection could also be provided by a kind of protective building for string inverters.
Another aspect that leads to an earlier end of life for inverters, according to both the Bern study and Heinzler’s experience, results from a widespread trend toward cost optimization. If the DC generator is set to be overloading by 40% or 45%, he sees more frequent malfunctions in operation than in systems where the oversizing is only 10% to 15%. “If I always drive my car at 220 km/hour, it will break down faster than if I always run at a comfortable speed of 120 km/hour,” Heinzler says.
Efficiency trade-off
Preventative measures for manufacturers could see them dimensioning the power semiconductors more generously, which prevents bondwire lift-off, explains Karin. However, it makes the devices both more expensive and less efficient.
Many shortcomings originate from trying to optimize project costs. Heinzler talks about how cable runs can be cut in half when project designers use a Y connector to put two strings on one MPPT [maximum power point tracking] input. But that is not without problems, he says. In one case he observed, this installation method was deemed fine by the manufacturer’s data sheet, yet Heinzler says he found that the devices were more prone to failure. The specific yields of the units also varied much more.
When Heinzler and his team removed the Y connectors, the susceptibility to interference decreased. His conclusion: “You have to keep a better eye on the balance between construction and operating costs. Especially due to the expected operating phase of 20 to 30 years. If you want to save a few more meters of cable here and save a few more plugs there come hell or high water, you’ll end up paying the bill.”
Anyone who includes the expected costs for repair or replacement of the inverters in the price will not build something like this, says Heinzler. He appeals to a “sound electrical engineering sense” when planning the systems. This includes not too much DC overloading and that inverters are taken out of direct sunlight. This increases the life expectancy of the inverters.
Life expectancy
Formulating an accurate life expectancy for devices is understandable from a business standpoint, but it’s not without its problems, Karin says. His impression is that manufacturers are gearing up to produce components with a life expectancy of 15 to 20 years. “Designing inverters means finding a fine balance between a robust, reliable product and one that is way too expensive,” he says. “Therefore, the assumption that an inverter lasts 10 to 15 years becomes a self-fulfilling prophecy.” If everyone in the industry makes the same assumption, manufacturers have little incentive to make their products more robust and durable.
On the other hand, manufacturers have been complaining for years that projects are too fixated on capex and thus opt against higher-quality components. And yet the industry has moved on. Technology consultant DNV produced a white paper noting that 15 years ago it was common to replace an inverter every five years. DNV estimates that the life expectancy of modern devices for ground-mounted systems is now just over ten years, which is reflected in warranty periods.
Continuous improvements are being made, and Klengel suspects that further progress can be made in proving and ensuring the longevity of inverters. She notes that the energy industry is placing higher demands on proving the reliability of components, which drives development. Klengel believes that competitively priced inverters with a life expectancy of 30 years, as is the case with solar modules, are technically feasible.
This content is protected by copyright and may not be reused. If you want to cooperate with us and would like to reuse some of our content, please contact: editors@pv-magazine.com.