https://www.pv-magazine.fr/2022/06/15/les-panneaux-photovoltaiques-se-mettent-aux-materiaux-biosources/
Les panneaux photovoltaïques se mettent aux matériaux biosourcés
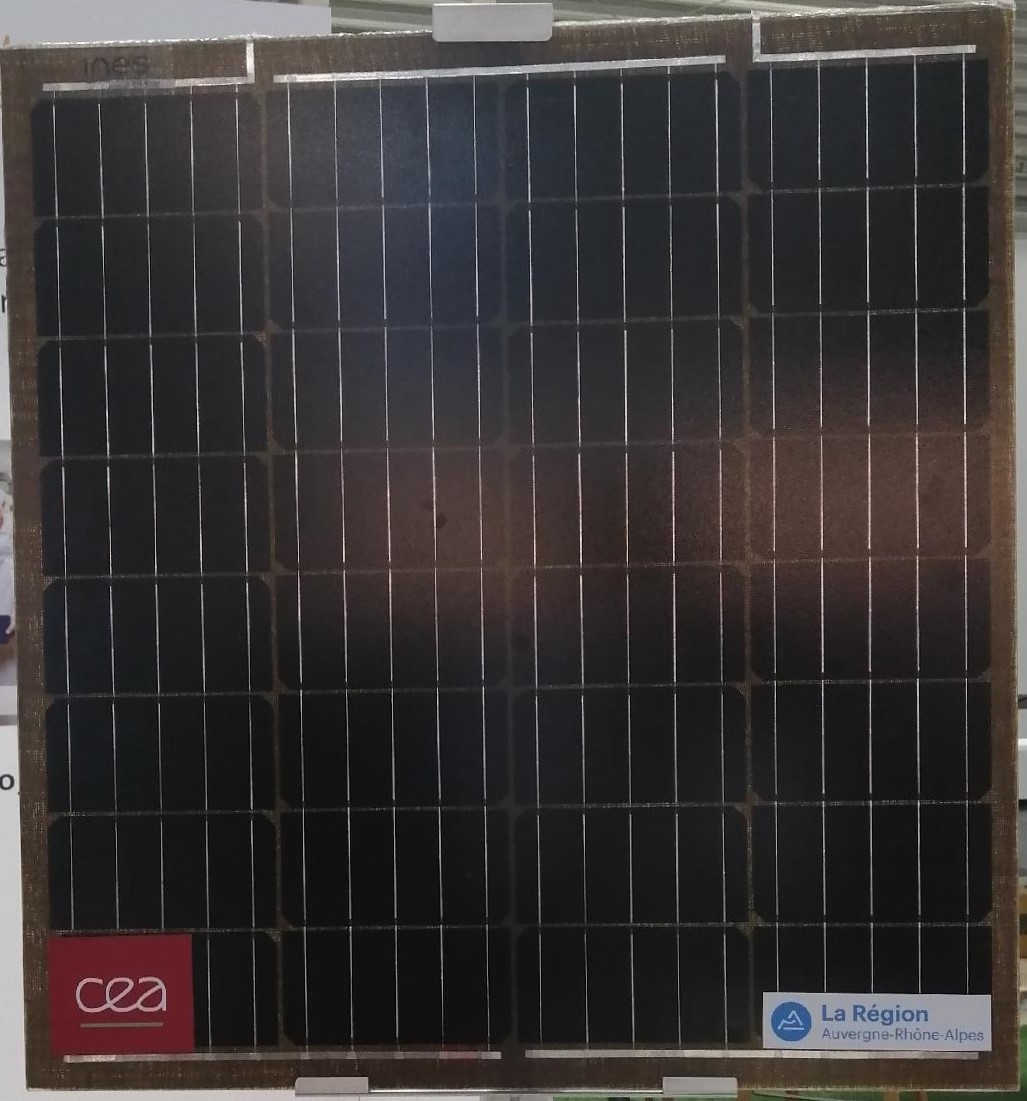
Module éco-conçu composé d’un verre de 2,8 mm réutilisé et d'un composite thermoplastique fibre de lin pour la tenue mécanique et la résistance à l’humidité.
Image : GD
« Nous en sommes persuadés : de la même manière que le bilan carbone et l’analyse de cycle de vie sont aujourd’hui devenus des critères essentiels dans le choix des panneaux photovoltaïques, le sourcing des matériaux va devenir un élément crucial en Europe dans les prochaines années », assure Anis Fouini, directeur du CEA-INES lors d’une interview avec pv magazine France. C’est pourquoi l’organisme de recherche travaille à l’incorporation de matériaux biosourcés dans les faces avant et arrière des modules et présente plusieurs démonstrateurs, fruit d’un travail de plus de deux ans.
Des matières éco-conçues sans modification de process
« Dans le cadre du mouvement de réindustrialisation de la filière solaire en France et en Europe, nous nous sommes intéressés aux différentes matières qui existent déjà industrialisées sur ces marchés, pour trouver celles qui vont permettre aux moduliers de fabriquer des panneaux qui répondent à leurs spécifications et à leurs impératifs de performances, de durabilité et de coût, tout en garantissant une réduction de l’impact environnemental », poursuit Aude Derrier, cheffe de service modules et systèmes, qui a dirigé les travaux de recherche.
Financé par la région Rhône-Alpes dans le cadre du programme Easy POC, le premier démonstrateur se compose donc de cellules HTJ intégrées dans un matériau tout composite. « La face avant est composée d’un polymère chargé fibre de verre, qui apporte de la transparence, détaille Aude Derrier. La face arrière est en composite à base de thermoplastiques dans lesquels a été intégré un tissage de deux fibres, le lin et le basalt, qui vont apporter de la tenue mécanique, mais aussi une meilleure résistance à l’humidité ». Le lin est sourcé dans le nord de la France, où tout l’écosystème industriel est déjà présent et le basalt est sourcé en Europe et tissé chez un partenaire industriel de l’INES. Grâce à cela, l’institut de recherche a pu montrer que le bilan carbone était réduit de 75 gr d’eq CO2 par W par rapport à un module équivalent de même puissance et le poids est également optimisé et est inférieur à 5 kg/m2. « Ce module s’adresse aux secteurs du PV en toiture, de l’intégration sur bâtiment (BIPV)…, relève Aude Derrier. L’avantage est qu’il est de couleur noire naturellement, sans avoir besoin d’une backsheet. Au niveau du recyclage, grâce aux thermoplastiques, qui peuvent être à nouveau refondus, la séparation des couches est aussi plus simple techniquement ».
Enfin, le module a été développé avec un pré-requis : que sa fabrication puisse être effectuée sans adaptation des process actuels. « L’idée est de pouvoir transférer cette technologie auprès des moduliers, sans investissement supplémentaire, assure Aude Derrier. Le seul impératif est de disposer de congélateurs pour stocker la matière et pour ne pas enclencher le processus de réticulation de la résine, mais la plupart des fabricants utilisent aujourd’hui du pré-imprégné et sont déjà équipés ».
Viser les problèmes d’approvisionnement en verre
Parallèlement, l’INES s’est penché sur les problèmes d’approvisionnement en verre solaire que rencontrent tous les acteurs du photovoltaïque et a travaillé sur la réutilisation du verre trempé. « Nous avons travaillé sur la seconde vie du verre et avons développé un module composé d’un verre de 2,8 mm réutilisé qui provient d’un ancien module, observe Aude Derrier. Nous avons par ailleurs utilisé un encapsulant thermoplastique qui ne demande pas de réticulation, qui sera donc facile à recycler et un composite thermoplastique avec fibre de lin pour la résistance ». Ne renfermant pas de basalt, la face arrière du module a une couleur naturelle lin, qui pourrait être esthétiquement intéressante pour les architectes sur de l’intégration en façade par exemple. De plus, l’outil de calcul de l’INES a montré une diminution de 10 % du bilan carbone.
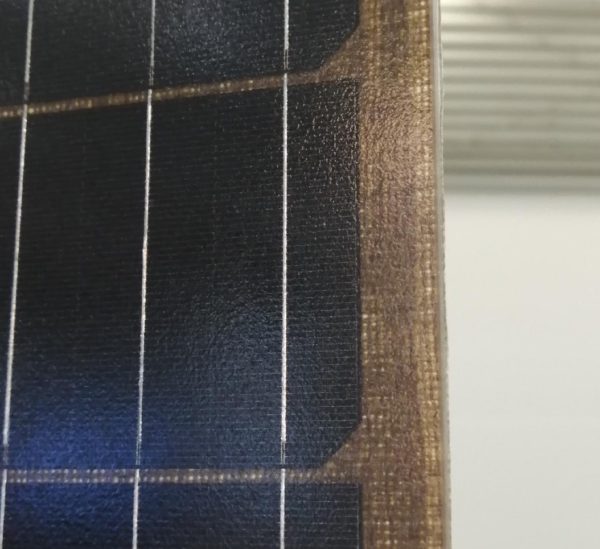
Image : GD
« Il est aujourd’hui impératif de remettre en cause les chaînes d’approvisionnement du photovoltaïque, abonde Anis Jouini. Avec l’aide de la région Rhône-Alpes dans le cadre du Plan de Développement International, nous sommes donc allés chercher des acteurs externes au solaire pour trouver de nouveaux thermoplastiques, de nouvelles fibres… Nous avons aussi réfléchi au process de lamination actuel, qui est très énergivore ». En effet, entre la mise sous pression, le pressage et la phase de refroidissement, la lamination dure d’ordinaire entre 30 et 35 minutes, avec une température de fonctionnement de l’ordre de 150 à 160 °C. « Mais pour les modules qui intègrent de plus en plus de matières éco-conçues, il est nécessaire de transformer les thermoplastiques autour de 200 à 250 °C, sachant que la technologie HTJ est sensible à la chaleur et ne doit pas dépasser les 200 °C », indique Aude Derrier.
Ne pas chauffer à cœur les cellules HTJ
Ce benchmark auprès des industriels a de fait abouti à un partenariat avec la société savoyarde Roctool, spécialisée dans la thermocompression par induction, qui permet une réduction des temps de cycle et de confectionner des formes selon les besoins du client. Ensemble, ils ont développé un module avec une face arrière en composite thermoplastique de type polypropylène, comme ceux utilisés dans l’automobile, auquel ont été intégrées des fibres de carbone recyclées. La face avant se compose de thermoplastiques et fibre de verre. « Le process de thermocompression par induction de Roctool permet de chauffer rapidement les deux plateaux avant et arrière, sans avoir besoin d’atteindre les 200 °C à cœur au niveau des cellules HTJ », décrit Aude Derrier.
Selon l’entreprise, l’investissement est moins important et le procédé doit permettre d’atteindre un temps de cycles de quelques minutes seulement en utilisant moins d’énergie. La technologie s’adresse aux industriels des composites qui auront alors la possibilité de produire des pièces en forme et de plus grande dimension et d’intégrer des matériaux plus léger et plus durables.
Avec un poids inférieur à 5 kg/m2, les applications visées pour le module pilote développé avec l’INES sont par exemple la mobilité, mais aussi le bâtiment, les centrales au sol, l’agrivoltaïsme… Le calcul de l’empreinte carbone est en cours.
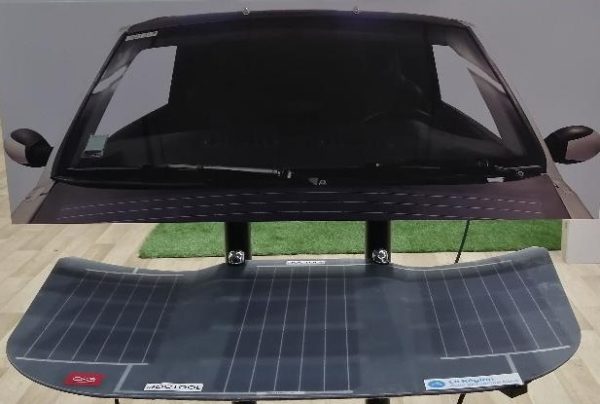
Image : GD
« Ces différents démonstrateurs ont été développés avec le souci que ces nouvelles solutions restent économiquement viables, conclut Anis Jouini. Aujourd’hui, avec l’augmentation des prix de l’électricité, nous pouvons nous permettre de proposer un module légèrement plus cher que ceux sourcés dans d’autres pays du monde, mais qui apporte un réel gain en termes sociaux et environnementaux, avec une matière sourcée et sécurisée en Europe. Une réelle carte à jouer pour la France et le continent européen dans sa recherche de différenciation et de valeur ajoutée.
Ce contenu est protégé par un copyright et vous ne pouvez pas le réutiliser sans permission. Si vous souhaitez collaborer avec nous et réutiliser notre contenu, merci de contacter notre équipe éditoriale à l’adresse suivante: editors@pv-magazine.com.