https://www.pv-magazine.com/2023/12/19/kpit-unveils-sodium-ion-battery-with-energy-density-of-up-to-170-wh-kg/
KPIT unveils sodium-ion battery with energy density of up to 170 Wh/kg
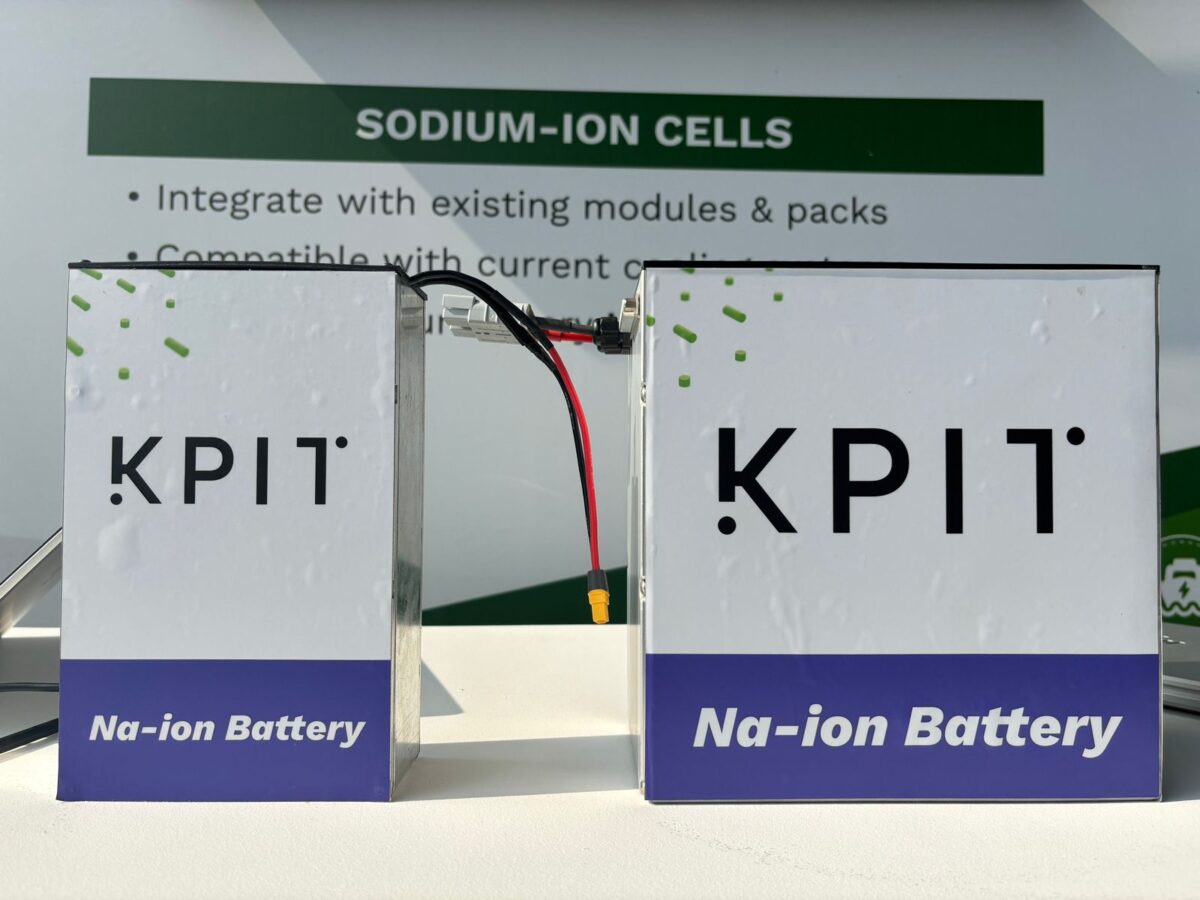
KPIT's sodium-ion battery technology has displayed 80% capacity
retention for 3000-6000 cycles.
Image: KPIT
While lithium-ion battery prices have this year returned to a downward trajectory, the interest in promising sodium-ion batteries has not waned. Most recently, India-based KPIT has developed a sodium-ion-based battery technology that it plans to license to prospective partners who could manufacture and commercialize this technology.
KPIT, which has a strong foothold in software development, integration, and validation for electrification programs for major OEMs in the global automotive space, has developed this technology in cooperation with the Indian Institute of Science Education and Research (IISER) based in Pune. The scientific team made contributions to material synthesis, characterization, and battery testing.
“Lithium deposits are concentrated in very few places in the world and lithium processing is concentrated in one or two countries. That is why about eight years ago we started looking at alternatives to lithium and we wanted to look at those alternatives which were ubiquitously available across the globe and that's why we started working on sodium-ion technology,” Ravi Pandit, chairman of KPIT tells pv magazine.
Thus far, the company has developed multiple variants of its sodium-ion technology with distinct performance characteristics and energy density ranging from 100-170 Wh/kg.
“When we started working on sodium-ion batteries, the initial expectation of energy density was quite low but over the last eight years the energy density has been going up because of the developments that we and other companies have been carrying out,” Pandit says.
The current iteration of KPIT’s sodium-ion cells has an energy density of 110 Wh/kg and feature carbon-based anode and polyanionic cathode.
“We soon realized multiple advantages of sodium-ion chemistry such as power density. You can charge a sodium ion battery 100% percent in less than 20 minutes with 3C charging and still you can get a long life,” Pandit says. “We have been testing the cells for about 4,000 to 5,000 cycles with such aggressive charging. However, in real world you don't have to do 3C charge all the time and you don’t have to charge to 100% all the time so the actual cycle life can be much higher.”
According to Pandit, KPIT also has batteries with an energy density of 135 and even 170 Wh/kg which are showing stable behavior. However, the latter ones have not been run for 3,000 cycles. “We believe that we can even go to way up to 220 Wh/kg with different combinations of anodes and cathodes, which comes quite close to the lithium-iron-phosphate lithium-ion chemistry,” Pandit says.
In addition to power density and long-life perks as well as faster charging than lithium-ion batteries, Pandit also underlines excellent sub-zero and high-temperature tolerance with minimal thermal management as another advantage of sodium-ion battery technology.
“Unlike lithium-ion batteries, sodium-ion can be discharged to zero and then safely transported,” he adds.
Popular content
Sodium-ion technology has several use cases for automotive and mobility, especially for electric two and 3-wheelers and commercial vehicles. It also has promising applications in stationary deployments, such as UPS backups and grid storage, as well as in the marine and defense sectors.
“When we started, we were mostly looking at electric vehicle applications for sodium-ion technology because our key focus is on urban mobility,” Pandit says. “We see great possibilities for this technology is shared transportation, but also in personal vehicles. Combining sodium-ion batteries with fuel cells is particularly interesting for long-distance heavy-duty application.”
Since KPIT has developed the chemistry ground-up, it can readily tune it to different types of applications. “If you were to look at an energy density of 60 or 70 Wh/kg per and at charging at 1.5 C then you can easily expect 20,000 charge-discharge cycles which would make it a great fit for grid-scale storage applications,” Pandit says.
KPIT has already established a network of supply chain partners and is now actively looking for manufacturing partners, also among its OEM clients.
“Our technology was developed as a complete drop-in technology for the lithium-ion batteries, so we will need only small modification in the precursor stage or in the mixing stage to use the same manufacturing lines to produce sodium-ion batteries,” Pandit says. “This means that setting up a manufacturing plant can take anywhere between 10 to 12 months depending on the partner’s state of readiness so that is the time it will take for a launch in a commercial sense.”
According to Pandit, KPIT is already in contact with a company in Germany that does prototype manufacturing on a 10 MW production line and can be expanded to a gigawatt-scale.
“I believe sodium-ion will play a big role in the automotive sector even before 2030 and we’ll see significant scale in two years time,” he says. “In the stationary storage application, the possibilities are huge. Only pumped hydro will be able to match the price point of large-scale sodium-ion batteries.”
Before its latest technology announcement, KPIT was primarily engaged in the work on battery management systems, battery packaging, as well as the overall electric powertrain. In addition, it has also worked on fuel cells, which according to Pandit will be officially launched in the foreseeable future.
This content is protected by copyright and may not be reused. If you want to cooperate with us and would like to reuse some of our content, please contact: editors@pv-magazine.com.